Blacksmithing as a southern skill
One of the skills we use here is old style blacksmithing. Here is one of the knives I made out of my newly rebuilt shop.
Chuck
9/8/20245 min read
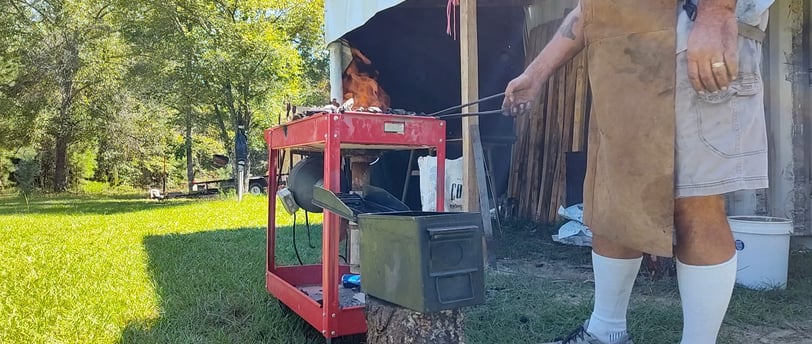
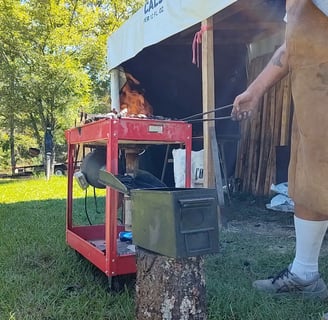
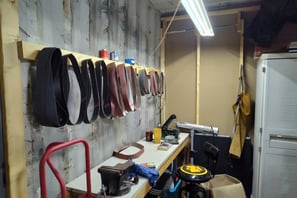
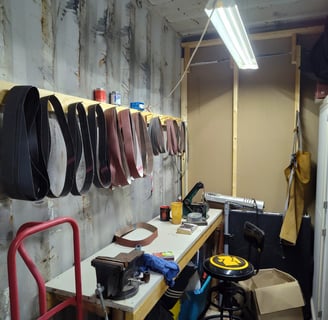
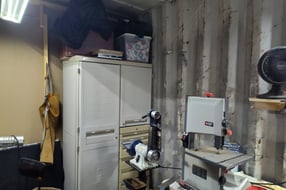
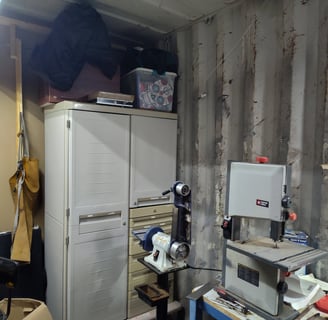
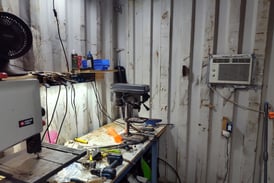
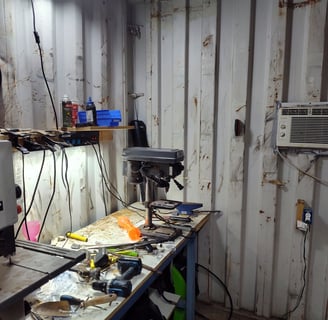
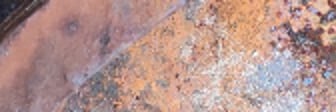

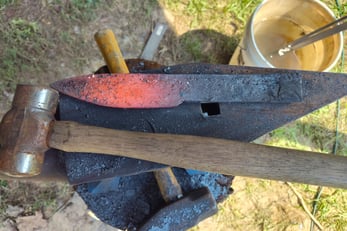
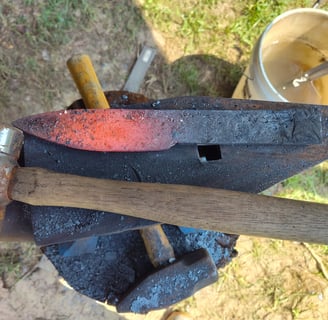
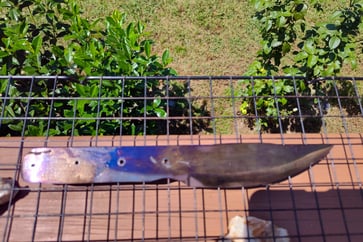
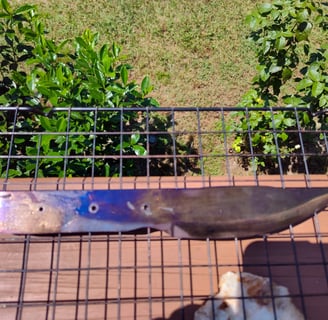
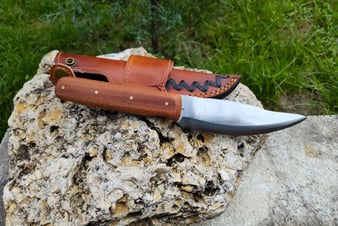
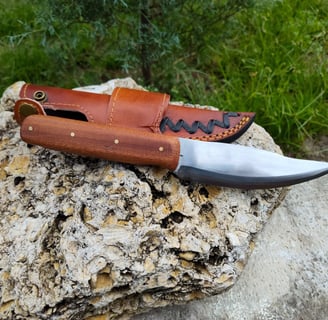
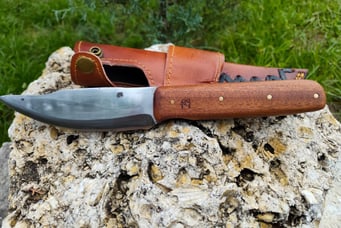
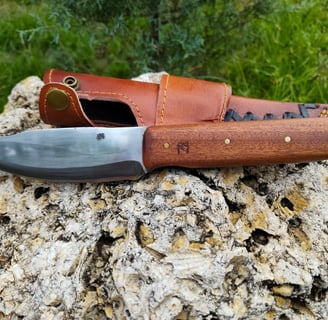
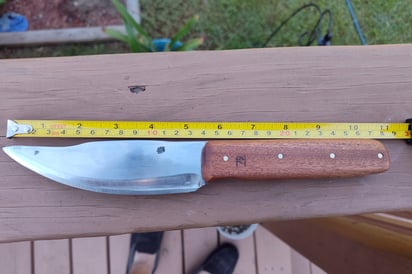
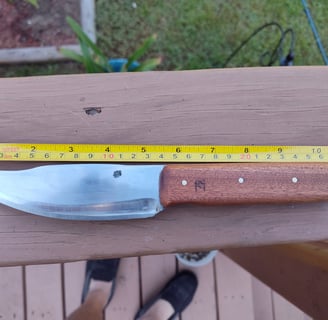
First off I want to apologize for not posting recently. My day job at the hospital as got to be bat sh---- ummm bat poop crazy with some HUGE changes coming. But that's neither here or there. For now.
One of the Southern Skills that is being lost to time is Blacksmithing. Sure right now my shop has all sort of nice modern power tools. (And its a bit messy when I took these pictures.
They do make the job a LOT easier. But it can be done with zero electricity. Sure some things will not be as "pretty" but they will be just as functional and durable as if I did the finish work on a belt grinder. Just about any tool you need on the homestead can be made from scrounged steel some coal an anvil and a hammer. I've made shovels from old disk harrows, froes and draw knives from old leaf springs. Campfire cook sets from just scrap steel lying around. And a lot of knives from railroad steel. Mainly the spring clips.
So today's post is going to be about a blade I made from scrounged steel. A railroad spring clip, wood from a broken piece of furniture some brass welding rod and of course coal and a lot of sweat.
This particular blade started as a railroad spring clip. These are fantastic pieces of steel, similar to 5160 spring steel but my gosh it is hard to start moving it!
Here that piece of steel has a rough blade shape. A bit more time on the anvil and it will be close to its final shape. With the current situation, meaning we have electricity, I'll do the final shaping on the grinder.
For some reason I can't embed the video of the quench, so here is the link to it on our new YouTube page.
https://www.youtube.com/watch?v=_PgeFOlzjDE
This video shows the quenching of the blade. You'll see that I take the blade out of the forge I touch it to the side of the forge, There is a magnet there. Steel when heated to about 1400 degrees loses it's magnetic properties. What I edited out is all the times I took it out and touched it to the magnet! Once the steel hits temperature, I pop it back in the forge for just a bit and into the oil. Once it cools a little I run a file over it to see if it hardened. If the file digs into the steel it's not hard and I redo it. If it skips its hardened and ready for tempering.
For this type of steel I put it in the oven, (Yup our kitchen oven) at 400 degrees for 2 hours. I do put an oven thermometer to be sure of the temp. This is done twice, with the blade allowed to cool completely between cycles. This is one thing they do not show on Forged In Fire. If this is not done, the blade is very brittle and can break. You see this alot on Forged in Fire when the blade fresh out of the oil and put in a vice and they try to straighten in. SNAP!! And then a lot of bleeped words! Tempering takes some of the hardness out and makes the blade more forgiving. A few times I left the colors on the finished blade, they look COOL! but it wears quickly and is prone to oxidation much faster.
After it cools then it's polishing, initial sharpening, fitting the handle and final polish and sharpening.
Here is the finished blade. The steel is Railroad clip Very close to 5160 spring steel. the handle is African bloodwood, I found a broken table at a thrift store for 10 bucks. Normally this wood is VERY expensive. And the pins are 1/8th inch welding rod that the ends are center punched to hold tight. I do use high strength epoxy, but SHTF Epoxy may be hard to find. I have used in the past, small machine screws that are counter sunk in the handle, or larger metal rods that I drill out a bit and peen them out to hold very tight. The bad thing is sometimes as the woods dries out the handle can become loose but is easily tapped tight again.
Here is some pictures of the finished blade.
Blades are a semi easy project. They build the skills need to forge more complex tools. Plus they are excellent barter material. A blade like this one will cost about $120,00 in current USD. But SHTF it may bring a lot of meat, vegetables, dry goods, medical supplies. You name it. It is a Southern Skill that needs to be learned.
I'm not an "expert" nor "master bladesmith.My grandfather taught me out on our ranch. He needed to fix a drawbar on a blow, and he didn't have a welder. But he had a forge an anvil and a hammer. And the skills to forge weld the bar back together. That is a real SHTF Skill. This blade will be in the near online store we're setting up, if anyone feels the need for a good heavy knife.
Chuck
September 8th 2024
Homesteading in The South
Southern Skills for The Modern Homesteader
Skills
SSFTMH1@gmail.com
© 2024. All rights reserved.